Your cart is currently empty!
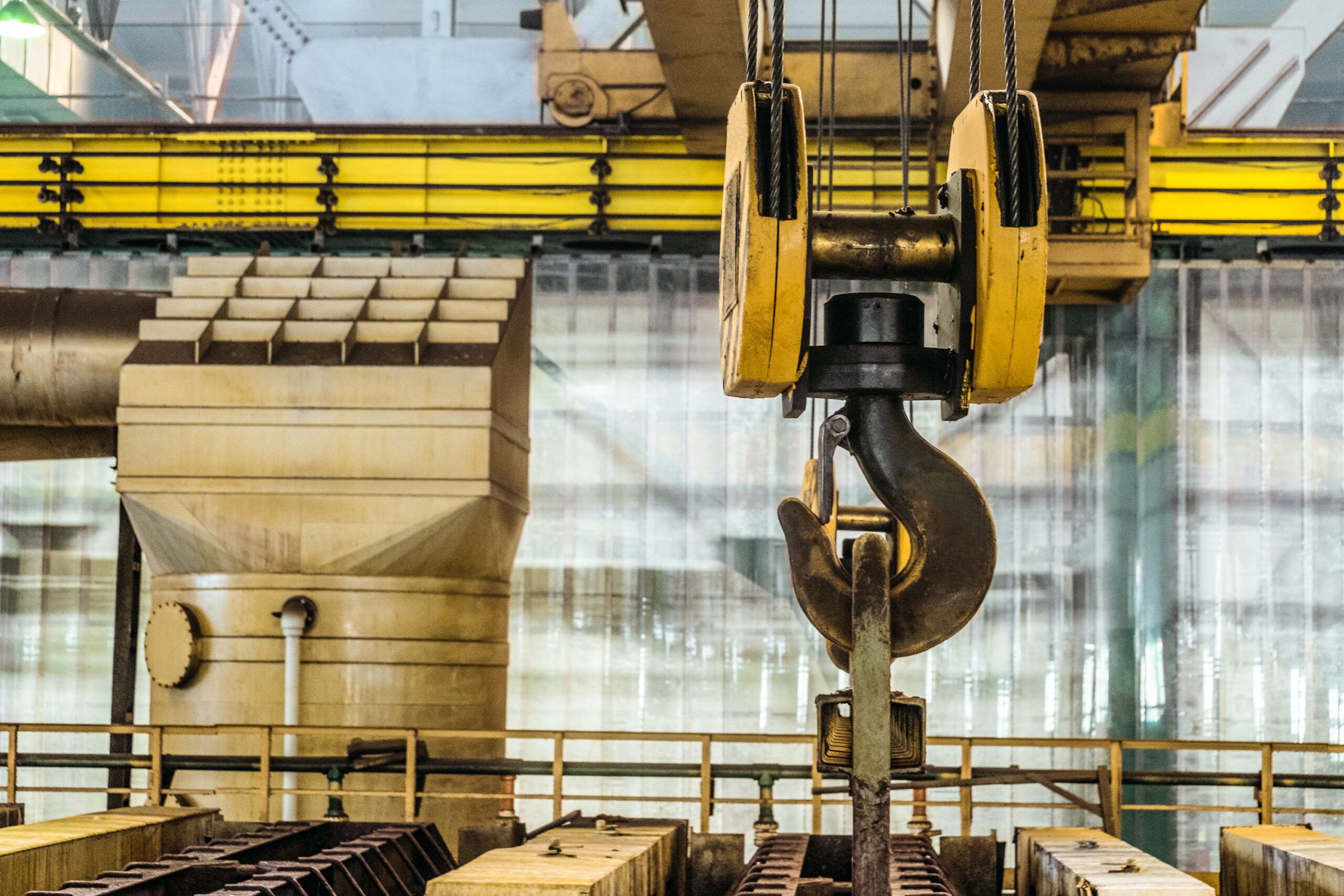
Pneumatic Hoists Pros/Cons
PROS/CONS of Pneumatic Hoists
What is a Pneumatic Hoist?
Pneumatic hoists are typically used in industrial production environments. These units feature either a rotary vane or piston driven air motor powered by compressed air. The greatest benefit of air hoists is that they have a 100% duty cycle rating, meaning unlike their electric counterparts, they never need to rest. Pneumatic hoists are however, only as good as the quality, pressure, and flow rate of the air that feeds them. One disadvantage of air hoists is that they consume a moderate to large amount of compressed air, which in turn calls for an air compressor capable of producing enough air flow to meet the cubic feet per minute (CFM) requirements of the hoist. Hoists operated below the rated CFM will not perform to their rated performance. Additionally, clean, dry, and lubricated air is critical to extending the operating life of an air hoist.
Pros
Source availability: Pneumatic systems require air to operate successfully. As a result of air being extremely abundant, and free, it is easy to restock the system.
Safety: As a result of pneumatic systems running on air, safety hazards are significantly reduced. There are limited occurrences of fires because air is non-flammable, and leakages in the system do not negatively effect the outside environment
Cost effectiveness: The initial cost of manufacturing a pneumatic device is minimal as a result of the low cost design materials. Plastics, zinc, and aluminum are all relatively affordable materials that are commonly found in pneumatic designs.
Cleanliness: As a result of the system being powered solely by air, the pneumatic device typically requires limited cleaning. Pressurized air constantly pushes out dirt or debris that get stuck in the system. If there is a blockage, the simplicity of the design also helps. Due to the limited amounts of tubes, the system can be easily disassembled and cleaned.
CONS
Adaptability: Unlike electric powered hoists, air hoists are bound to its location due to its attachment to hoses and compressors. Electric hoists are portable and can be moved to anywhere with a power source.
Control and Speed: Air is a compressible gas, which makes control and speed in a pneumatic system more difficult, in comparison to electric or hydraulic systems. When specific speeds are needed, additional devices have to be attached to the pneumatic system in order to procure the desired result.
Maintenance: Pneumatic systems are less durable due to moisture accumulation the system can freeze up. In order for the system to properly operate it must be lubricated with oil consistently. Be sure to use advanced air treatment and filtration systems so that all moisture is taken out prior to feeding the hoist. Rust may occur.
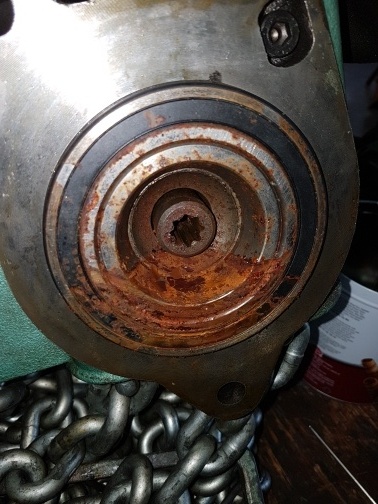
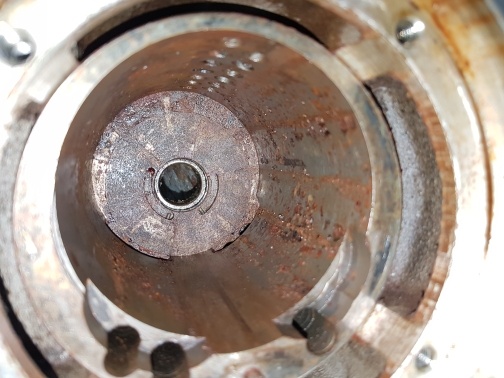
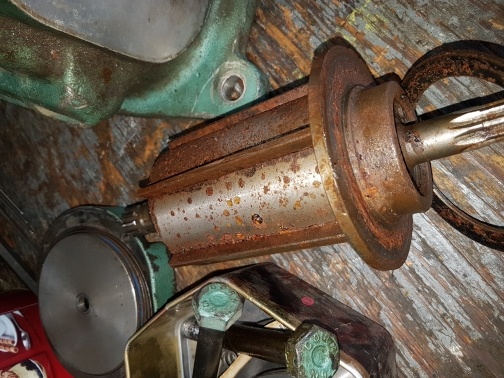
Safety: Pipes that feed the system air have the ability to move on uncontrollably on their own, which could cause serious injuries to those nearby
Environment suitability: Devices are known to fail over long periods of time due to the dampening of inside edges in the tubes. Additionally, systems cannot operate underwater and are sensitive to changing temperatures and vibrations
Loudness: Pneumatic systems are the loudest type of designs that power machines. Actuators that run the system are the source of the noise and are sometimes placed in a separate room to limit sound pollution.
Toxins and chemicals: Sometimes, pneumatic systems use hazardous chemicals in their design. This can result in accidental launches of chemicals into the air, which can be harmful to the surrounding environment.
Maintenance for a Pneumatic Hoist
Maintenance Intervals
The maintenance interval chart is based on intermittent operation of the hoist eight hours each day, five days per week, in an environment relatively free of dust, moisture and corrosive fumes. If the hoist is operated almost continuously or more than eight hours each day, more frequent maintenance should be performed.
Start of each shift | Semi-Annual Maintenance | Yearly Maintenance |
– Make a thorough visual inspection of the hoist for damage. | – Inspect the brake. | – Inspect the hoist gearing, shafts and bearings for wear and damage. |
– Do not operate the hoist if damaged. | – Clean or replace parts as required. | – Repair or replace as necessary. |
– Operate the Hoist in both directions. | – Adjust brake as necessary. | – Check all the supporting members, including the suspension, fasteners, nuts, sheaves and rigging, etc. for indications of damage or wear. |
– Hoist must operate smoothly without sticking, binding or abnormal noises. | – Repair or replace as required. | |
– Check the operation of brake. |
Please Refer To Electrical Hoist Page for Exact Maintenance Intervals